And when I say 'good time' please do accept that as a relative comparison to say burger flipping, making lattes for annoying customers, or working the graveyard shift at the Kwickie Mart.
I caught this really interesting piece on Forbes, DOT's New Curb on Driver Hours Is Hurting Productivity, Truckers Charge, that while seemingly a dull piece about changes in Federal work rules governing working hours for commercial truck drivers that would only be interesting to say actual truck drivers and trucking company operators, actually to me reveals much about the future of work and the automation of work here (and likely everywhere).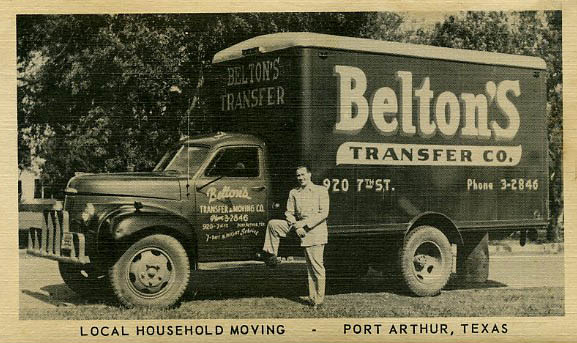
First, take a look at the main point of the piece in Forbes, then a take from me on why this matters more generally, (and why robots are involved, naturally).
Rules limiting the number of hours that commercial drivers can be on the road are resulting in a marked drop in productivity, trucking companies claim.
The latest Hours of Service (HOS) rules were put into place on July 1, 2013 by the Federal Motor Carrier Safety Administration, part of the U.S. Department of Transportation. They state that drivers of commercial motor vehicles can be on the job for a maximum of 11 hours, following 10 consecutive hours off duty. They must take a minimum 30-minute break during the first eight hours of a shift. Their maximum average work week is capped at 70 hours, down from the previous limit of 82 hours.
The trucking industry fiercely opposed the tighter rules during public hearings, but to no avail. Today, a trucking company whose driver exceeds the limit by more than three hours can be fined $11,000 per offense, and the individual driver faces civil penalties of up to $2,750.
During the public comment period, truckers warned that the rules would cut deeply into their productivity. Now, they say, that is precisely what has happened.
Schneider National, one of the nation’s largest truckload carriers, predicted back in February of 2011 a productivity drop of between 3% and 4%. Four months after implementation of the HOS rules, Schneider is reporting declines of 3.1% on solo shipments and 4.3% on team shipments.
Pretty straightforward, right?
The Feds tighten up the rules around how long in a day and for a week that commercial truck drivers can be behind the wheel, thus creating an artifical constraint on labor supply, (I am not going to even try to get in to the debate about whether or not this change in rules was needed or makes sense, because I simply do not know), and the trucking companies begin to feel the pinch in lost output and productivity.
The simple solution, and the reason this story was interesting to me, would be for the operators to simply hire more drivers. But it turns out, this would not be an easy solution at all.
From a related Bloomberg piece on the changes in truck driver working hours regulations:
Adding more drivers to payrolls will be a difficult undertaking. The industry was 158,000 drivers short of what it needed to meet demand in the second quarter, according to (trucking industry analyst firm) FTR Associates.
The shortfall probably will widen by the end of this year to 251,000 truckers, the biggest deficit in nine years, and reach a record 338,000 by the end of 2015, according to FTR’s Driver Shortage Surplus gauge. The economic expansion and higher turnover help explain the industry’s labor shortage.
“Every cost gets passed down,” said Sean McNally, a spokesman for the ATA, an Arlington, Virginia-based industry group. “As the labor market tightens and as demand for drivers goes up, typically wages go up as well. The competition is already fierce for good drivers. This is only going to increase that competition.’
An industry and job function that had been already been facing labor shortages, (Mama's don't let your babies grow up to be truck drivers), and now feeling even more of a pinch from a forced reduction in labor capacity (in the name of safety, at least according to the Feds). In the short term, it seems like wages are going to have to rise at least some in order to get more people recruited into becoming commercial truck drivers. Of course the operators, (and their downstream customers), don't like to hear that. Increased wages means lower profits.
But longer term, it seems like while we have read lots and lots over the last two years or so about self-driving cars, the real 'killer' application of the self-driving technology is going to be for commercial trucking.
If the big trucking companies are looking at labor shortfalls that estimates say will increase to over 300,000 in a couple of years, then something is going to have to break. And applying the self-driving technologies to a very real and growing economic problem will provide the necessary incentive to push the development of these technologies into higher gear (apologies for the very unfortunate pun).
It will probably be a pretty good time for the next few years to be an experienced commercial driver. But after that, probably not so much, as automation or self-driving or whatever it ends up being called will eventually put 'truck driver' on the list of careers that end up being displaced by technology.
Which of course will make it even more difficult for the trucking companies to find the human drivers they need today, who will begin to sense their days are numbered from the first moment they get behind the wheel.
Happy motoring.